When the front windshield was removed I discovered some rust holes underneath the window rubber.
Oww, I'm not a very good welder... But it would appear I was in luck knowing a qualified welder :-). Myk, a friend from work happens to be a first class welder. I could borrow a Gasless welder from another friend at work and last saturday and sunday Myk started welding the holes in the frame of the front windshield.
 |
Left side frame front windshield with rust holes |
 |
Right side frame front windshield Volvo 122S with rust holes |
 |
Gasless welder Weldmate T100P with 0.8mm wire |
 |
Myk building up a weld to fill the rust holes |
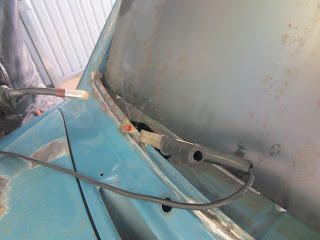 |
Built up weld in frame front windshield Volvo 122S |
 |
Right side frame front windshield built up with weld |
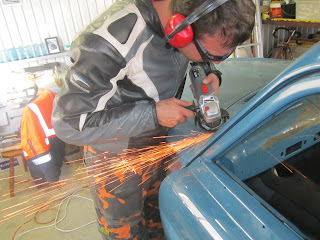 |
Myk grinding the built up weld |
 |
Welds frame front windshield grinded |
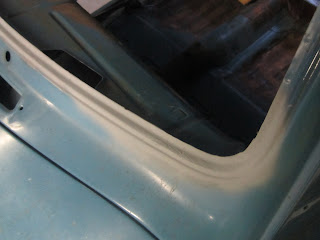 |
Zinc spray |
Next thing was the Anchorage for the rear bumper on the left side. It was way more work than I thought. First We had to remove the old rusted one, it was spot welded to the spare wheel well. After grinding for an hour or so the old one was removed and the surface was smooth enough to weld on the new anchorage. In order to tack it on exactly the right spot we took the rear bumper and while I was holding it in the right position Myk tacked the anchorage to the body. After welding I sprayed zinc primer on the weld and surrounding bare metal. The next day I covered it with a thick coat of bitumen/ sound deadener.
 |
Old rusted anchorage spare wheel well |
 |
Grinding down old anchorage |
 |
New anchorage spare wheel well Volvo 122S |
 |
Anchorage tacked after the bumper was aligned |
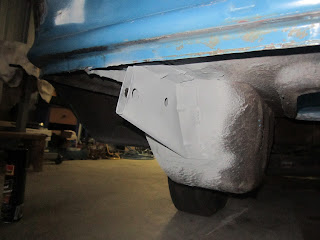 |
Anchorage with zinc primer |
 |
Thick coat of bitumen on anchorage spare wheel well Volvo 122S |
 |
Ready - Rear bumper Volvo 122S properly aligned |
Next time Myk is going to weld the front and right front fender.
Excellent stuff, you must be pretty skilled to do such thing, i can never imagine to do something like on my own, i always go to my local area auto shop for jobs like these.
ReplyDelete